Total CI Info - eliminate waste, reduce costs and maximize partner value
Total CI Info - eliminate waste, reduce costs and maximize partner value
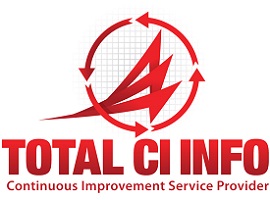
To understand the company Total Continuous Improvement Information (TCII) you need to understand the background of Scott Bensen, the company founder and president. Scott Bensen’s background in continuous improvement started when he received his undergraduate degree in Applied Physics. While studying for this degree, Scott worked with advanced physic techniques, learned how to get accurate measurements using advanced equipment and got his introduction to statistics and data analysis in propagation of error: meaning- how well do we know the errors in our measurements.
After earning his degree, Scott spent three years working for 3M. He worked on various projects, such as process development for the first erasable laser disc, which looked like a CD but was basically the hot mass storage device of that time.
Scott went back to school to get his master’s degree in statistics. He was able to work and learn from George Box and Normal Draper, who are the gurus of advanced statistical experiment data analysis. His Master’s degree was with an emphasis in quality and productivity, which shaped his career towards studying continuous improvement.
After completing his master’s degree, Scott spent 15 years with Rockwell Automation. He completed a lot of great work during his time there, but one of the highlights was designing a Quality Information System (QIS) that was recognized on a national level. That Quality Information System was a corporate quality reporting tool with the ability to reveal not only the defects but drill down to the actionable data to help correct those defects. During that time, Scott was also involved with the ISO 9001 program. ISO 9001 is based on the plan-do-check-act methodology and provides a process-oriented approach to documenting and reviewing the structure, responsibilities, and procedures required to achieve effective quality management in an organization.
In 2008, Scott opened TCII with the goal of improving the quality of processes, systems and data in all sizes of business. Over the years, the terminology for this type of business has changed - you may have heard it as: Quality Assurance, Quality Control, Total Quality Management, Business Process Improvement, and now Lean and Six Sigma. But for Scott- improvement has always been at the heart of his business.
Each year, TCII commits to staying on-top of the emerging best practices in Continuous Improvement using Lean and Six Sigma methodologies. This ensures that TCII can be the most impactful partner possible, with deep understanding of how to use Continuous Improvement tools to enhance an organization's culture and leadership.
TCII has found a lot of success - including speaking at four national conferences regarding quality and continuous improvement, developing and implementing 25 custom data collection system clients, and maintaining the ASQ Six Sigma Black Belt certification which is one of only two which require recertification.
TCII understands that the goal of every business is to provide value to their customer. The way value is measured is often the quality divided by the cost.Here is a blog that I wrote to give you a better understanding of what quality means. To maximize the value your business has you can increase the quality, decrease the cost - or both! TCII helps you get those results.
TCII clients are driven by results, from start-up companies to mature organizations, they know the importance of keeping one step ahead of the organization. That is why TCII aims to partner with organizations who want to eliminate waste, reduce costs and maximize the value their partners can provide to their customers. How do they do this? By developing data-driven, sustainable improvement strategies that enhance both the value delivered to customers AND the organization's bottom line.
TCII starts by evaluating the business culture to better understand the needs of the owners, employees and customers. Then when they understand the context of the business and needs of the organization, they implement continuous improvement techniques and evaluate operations to help make data-driven decisions that get measurable results.
TCII has a proven track record of developing solutions with fact-based data. They build it in so that long term improvement is objectively tracked - after all, you can’t manage what you don’t measure.
To learn more about TCII, please visit www.totalciinfo.com or call Scott at 715-892-0450.